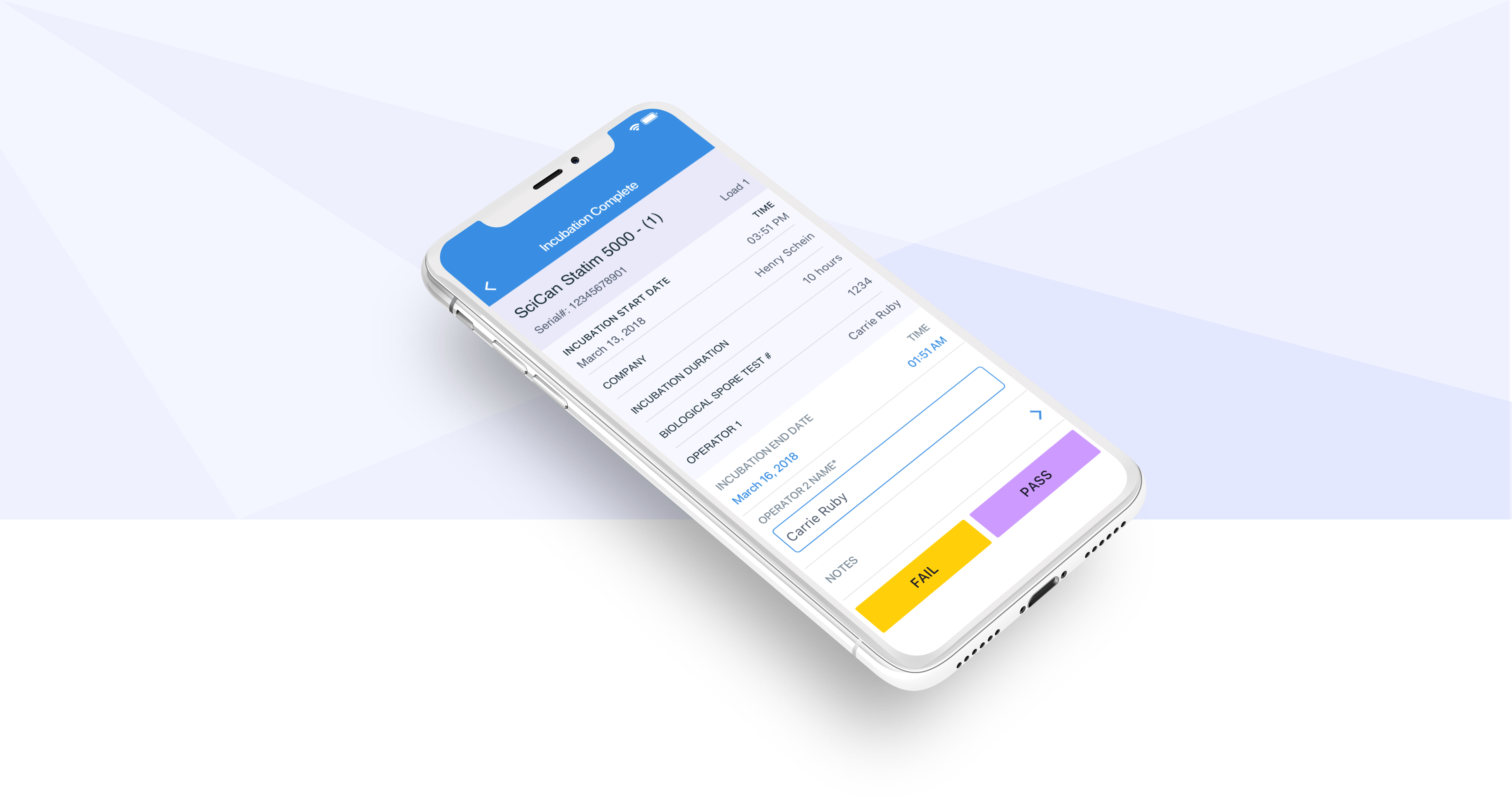
Think back to the last time you were in a dentist chair. Those shiny metal tools arranged neatly on a tray on blue paper. It's probably uncomfortable to think about... but are those really clean? They were in someone else's mouth... who knows how long ago. How do dental practices sterilize these things? With a revolving door of patients, practice owners are particularly concerned about proper equipment sterilization to avoid the risk of disease transmission between patients, steep fines and potential office closure. Our goal is to alleviate this anxiety by designing a tool for dental teams to record proof of compliance with government health standards.
Sowingo - 2018
iOS App
Sketch, Invision, Adobe Illustrator
Practices need to ensure their autoclave machines are functioning at peak capacity, but they are concerned about complying with government health standards because of the ambiguity surrounding infection control requirements and best practices.
Research, UX, UI, visual design, research, and testing were part of my process. Understanding infection control regulations and the primary user’s workflow within the office informed the design and interactions. Apart from the user, stakeholders, development, customer service & sales were part of the feedback loop. The App is currently available on the App Store.
Infection control is a process that tests autoclave machines (or other machines) to ensure equipment is sterilized adequately between each patient.
This project initially began with a plan to iterate over the existing web app and build a mobile version. We decided to proceed with a complete redesign because after evaluating the App we found that users, although excited by digital record keeping, were reverting to written log sheets. They were clearly not getting the assurance of safety they needed to create and store these records on Sowingo. Dental staff answer to the practice owners who inturn are held respoinsible in case of government audits.
Dental offices have dedicated sterile rooms, and after the equipment is washed and disinfected, it is wrapped and placed in an autoclave machine. The autoclave heats up to a target temperature and pressure for sterilization to be achieved.
Dental Assistants run numerous daily redundancy tests on the autoclave machine, and the results of these machine tests (Pass or Fail) are used as proof of infection control compliance. For the purpose of this case study, we will focus on Biological/Spore Test:
“BIs or spore tests are the most accepted means for monitoring of sterilization because they directly assess the procedure's effectiveness in killing the most resistant micro-organisms.”
(Royal College of Dental Surgeons of Ontario (RCDSO) Guidelines)
Once the purple spore test comes out of the autoclave, it is put into an incubator. If all the spores have not been killed the colour changes to yellow and the test fails. These steps highlighted the potential touchpoints with the App.
Can we design a familiar and functional experience within the dental team's work-flow by:
Before diving in and visiting Dental Offices, I did some research to get a base understanding of the process. I also wanted to plan our approach to gathering information and feedback. Even though our focus is on the primary user, there are external factors that affect their behavior. The staff has to adhere to guidelines from the CDC and Health Canada and we needed to account for this when designing the tool.
We identified all the "required information" using online government resources (CDS and Health Canada). We also spoke to 9 accredited Infection Control Experts hired to audit and train dental offices on best practices.
At 5 dental practices, we observed their infection control flow (refer above) and how they maintained their records. All users have paper logs to record their test results and keep them in storage for 2 years or more depending on the province or state. Based on conflicting conversations, it was apparent that there was a lack of clarity on the dos and don'ts:
“We went to an infection control seminar, and they say that we have to do a Spore Tests once a week”
-(Office 2, Toronto)
“On the website it says we have to do a Spore Test Every Day”
-(Office 3, Toronto)
Here are some of the things we learned from our research:
At this stage, from our research, we had gathered the data we needed to capture and clarity on what the users were trying to achieve. We turned our attention to creating the experience. We chose to go mobile first this time around because our research showed that desktops were less accessible in dedicated sterile rooms.
As highlighted above, there are predefined steps that the user takes when testing their autoclave machines. We explored several versions incorporating these steps.
We divide the flow into 3 stages, the same as the number of phases in their testing process.
Through testing, we found that returning to the App three times was excessive with offices being as busy as they are.
We did alternate versions by reducing the number of steps to two and combining the data from the Sterilization Cycle and Incubation Cycle (begin).
With testing we iterated over the flows and wireframes. The main task is to add a new test.
It took a few iterations to ensure the flow worked for the staff and fit into their environment:
We consistently received feedback from our users and made changes to clarify and streamline the system. We made small tweaks for more flexibility with manual overrides of load numbers which were initially designed to increment automatically. We also added features based on the ability to export and share tests.
We made sure to reconnect with the infection control experts to make sure we were building a product that took all the uncertainty off our user's plate.
The infection control section was built as a free feature to create some stickiness and complement the inventory management. We found an increase in new practices joining Sowingo interested in using Sowingo primarily to track their infection control records. With existing users, we had to rebuild some trust because of their previous experience using the tool. This made for a slower transition with some users still keeping their written logs.
After the redesign and release, The Organization for Safety, Asepsis and Prevention (OSAP) partnered with Sowingo, providing another layer of trust in the software.
One of the challenges for Sowingo now is monitoring the regulations and ensuring that the App reflects any government changes. Users now rely on us to ensure they are recording all the information they need. This App will likely require a lot of up-keep.
I found that our newest users reached out to us with questions and feedback about the app. Further improvement to the app will mend the break in the current experience so the user can manage all their machine names and types on the mobile app. This functionality was not included in the initial release.
There is so much value in time and effort saved when research is applied to validate assumptions. Initially, this app was designed for users in both the USA and Canada. We learned early on through research that offices in the USA don't need to maintain records because their testing is handled externally. We may not have made significant changes, but we were able to focus on right users rather than try and accommodate everyone.
Empathy is part of the process. All of Sowingo's tools are designed for the primary user who isn't the customer or decision maker. A majority of the time, the primary user doesn't have a vested interest in using the product. They need to feel like they are taken care of and not feel like this is "more work" for them.
As always, I’m grateful to all the dental offices that welcomed me back several times for my research. I also really appreciate the infection control experts sharing their knowledge and feedback and helping us build a tool that allows practice and their patients stay safe.